What basic refractory materials are needed for steelmaking? Steelmaking furnaces mainly use alkaline refractory materials. The main basic refractories used include magnesite bricks, magnesia-chrome bricks, and magnesia-calcium bricks, magnesite refractory bricks, etc. Electric furnace bottom ramming material, tundish coating material, electric furnace gunning material, converter gunning material. Hot repair material for converter, dry material for working layer of tundish. Main alkaline refractory materials such as magnesia refractory mortar.
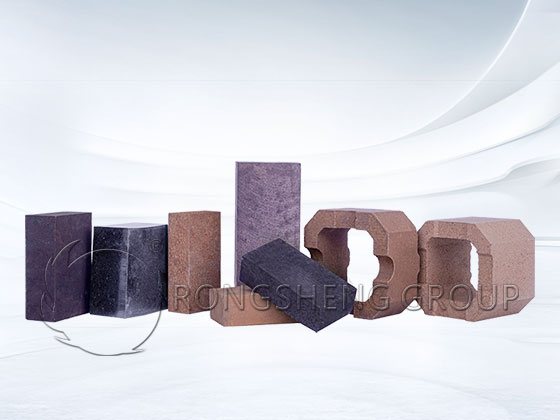
Basic refractories for steelmaking furnaces
What are the main products of alkaline refractories? The main products of basic refractories are magnesia bricks, magnesia chrome bricks, and magnesia calcium bricks. Magnesium ramming material, spreading material, gunning material. Magnesia refractory clay, dry material. Periclase spinel bricks, magnesia chrome bricks, magnesia iron spinel bricks, magnesia calcium zirconium bricks, magnesia aluminum iron chrome spinel bricks. Fused magnesia bricks, high-purity magnesia bricks, sintered magnesia bricks, directly bonded magnesia-chrome bricks, and magnesia-zirconium bricks. Dead-burned magnesia, mid-grade magnesia, high-purity magnesia, fused magnesia, sintered magnesia-chrome sand, high iron sand, magnesia-calcium sand, and other main basic refractory materials.
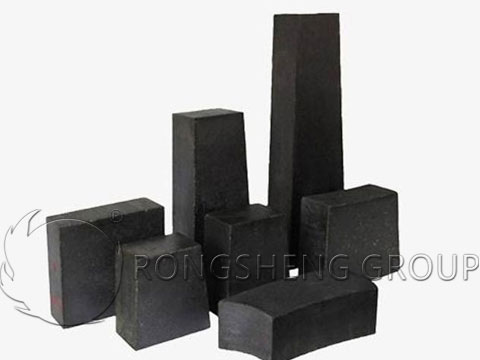
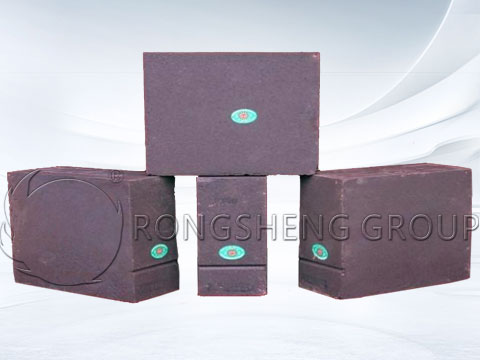
Magnesia bricks are commonly used. The manufacturer of magnesia refractory bricks pointed out that magnesite bricks uses are widely used in steelmaking furnace linings, ferroalloy furnaces, and mixed iron furnaces in the iron and steel industry because of their good high-temperature performance and strong resistance to alkaline slag. Non-ferrous metallurgical industrial furnaces, such as copper smelting, lead, zinc, and Sid furnace lining. Lime kilns in the building materials industry. Glass industrial regenerator lattice and heat exchanger. High-temperature calcining kilns, shaft kilns, and tunnel kilns in the refractory industry. Magnesite bricks containing more than 80% to 85% of magnesium oxide have good resistance to alkaline slag and iron slag, and their refractoriness is higher than that of clay bricks and silica bricks. magnesite bricks uses. Mainly used in open hearth furnaces, oxygen-blowing converters, electric furnaces, non-ferrous metal smelting equipment, and some high-temperature equipment. Features Inorganic non-metallic materials with refractoriness higher than 1580°C.
Performance of high-quality magnesia bricks
- Since the main crystal of magnesia brick is strongly alkaline periclase, it has high density, low water content, high molding pressure, low apparent porosity, and high bulk density. Therefore, magnesia bricks have the characteristics of a multi-mineral composition, strong alkalinity, and high density.
- Magnesia brick is a typical alkaline refractory material, which has a strong ability to resist alkaline slag erosion.
- The melting point of periclase is as high as 2800°C, so the refractoriness of magnesia bricks is also very high, generally above 2000°C.
- The load softening temperature of magnesia bricks is much lower than the refractoriness, about 1500 ℃.
- The thermal conductivity of magnesia bricks is good, but the thermal conductivity decreases significantly with the increase in temperature, that is, magnesia bricks have good thermal conductivity and low thermal insulation.
- The thermal expansion of magnesia bricks is relatively large, and the linear expansion coefficient increases with the increase in temperature. The thermal shock stability of magnesia bricks is poor, and the number of water cooling is only 2-3 times.
The magnesite bricks of Rongsheng refractory brick manufacturers are generally divided into two categories: sintered magnesia bricks and chemically bonded magnesia bricks. Magnesia bricks with high purity and firing temperature are called directly bonded magnesia bricks because of the direct contact of periclase grains. Bricks made from fused magnesia are called fused rebonded magnesia bricks.
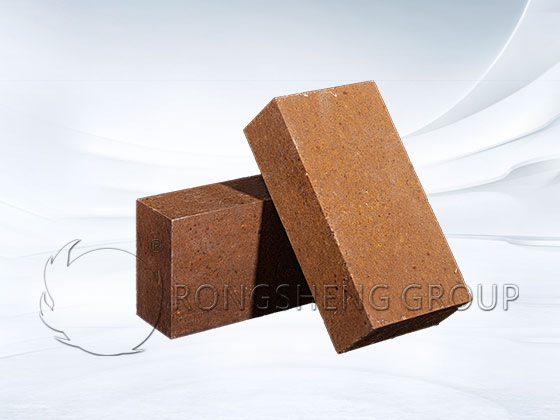
The basic refractory mixture of the AC electric furnace bottom and slope working layer should meet the conditions
- (1) High resistance to hydration and crystalline transformation of 2CaO·SiO₂ and resistance to 3CaO·SiO₂ decomposition.
- (2) The construction is quick and easy.
- (3) The furnace can be started immediately without drying or heating.
- (4) The sintering performance is high, and sufficient ceramic bonding can be obtained.
- (5) The density of the construction body is high and the porosity is low.
- (6) High volume stability and small shrinkage.
- (7) High corrosion resistance.
- (8) High resistance to mechanical stress and thermal stress.
Improving the service life of the lining of the steelmaking furnace
With the technical progress of the application of refractory materials in the converter, the furnace age is an important technical indicator for converter steelmaking. Increasing furnace life not only reduces production costs but also improves production efficiency. The refractory material of the converter lining is the main factor affecting the furnace life. In recent years, through the development and research of scientific and technical personnel, the life of the lining has been significantly improved, and the unit consumption of refractory materials has been reduced to 2-0.38 kg/t steel.
Rongsheng refractory manufacturer
Rongsheng Refractories Manufacturer is a powerful manufacturer of refractories for steelmaking. Rongsheng not only built its own refractory brick production line but also built an environmentally friendly fully automatic monolithic refractory production line. Our refractory products have been sold to more than 70 countries and regions all over the world. Our refractory products for steelmaking furnaces, high-alumina bricks, magnesia bricks, magnesia-chrome bricks, magnesia-carbon bricks, etc., have been used in customers’ high-temperature furnaces, and the furnace repair period has been extended compared to before. To purchase high-quality refractory materials for steelmaking furnaces, please contact us. While we help steelmaking furnaces solve the problem of refractory lining materials, we can also save production costs for you. Quote now! Chance to get a free sample.