In China, the P-S converter is currently the most widely used copper smelting furnace in the copper smelting industry. To know how to choose refractory materials prices for converter linings for copper smelting, we first need to understand the smelting characteristics of copper smelting converters.
Smelting Characteristics of Copper Smelting Converter
There is a large amount of SO2 gas in the atmosphere of the copper smelting converter. Since the ore is a sulfide mine, the intermediate product in smelting is a sulfide melt. Therefore, a large amount of SO2 gas is generated during smelting and blowing. The melt encountered is not only oxide slag, metal melt, but also sulfide melts matte or matte (copper matte or nickel matte). Moreover, the melting temperature of these melts is much lower than that of the melts encountered in the steel industry, and the fluidity is very good.
Copper smelting converter slag is FeO-SiO2 series slag, and the amount of slag is large. Since sulfide ore and matte contain a large amount of iron sulfide, in order to remove iron, FeS is oxidized to FeO during smelting and blowing. Therefore, SiO2 must be added to make slag, and the slag composition is mainly FeO and SiO2. In addition, since the ore and matte do not contain high levels of copper or nickel, the amount of slag is very large during smelting and blowing.
The converter for converting copper or nickel is an intermittent production furnace. The temperature in the furnace fluctuates greatly, and the temperature of the tuyere and tuyere area not only fluctuates greatly but also frequently. Therefore, refractory materials are required not only to be resistant to erosion and erosion but also to be resistant to thermal spalling and structural spalling. However, structural spalling is a weakness of refractory oxide materials, and it is difficult to overcome this weakness. Therefore, the life of the converter lining is generally lower than that of other non-ferrous smelting furnaces.
Selection of Refractory Materials for Copper Smelting Converter
Figure 1 shows the solubility of various refractory materials Al2O3, MgO, Cr2O3, ZrO, and CaO in iron-silicon slag at 1500°C. The amount of liquid phase formed at 1600°C by mixing magnesia-aluminum spinel (MA), magnesia-chromium spinel (MK), and their composite spinel and iron-silicon slag with different compositions. Some test results such as the amount of magnesia-aluminum spinel and magnesia-chromium spinel dissolved in the liquid phase were analyzed. It is also believed that magnesia-chromium spinel (MK), chromium trioxide (Cr203), and Cr203-containing refractories are better resistant to corrosion by iron and silicon slag.
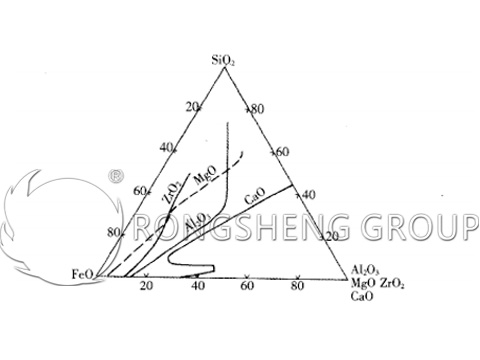
In summary, the refractories for copper smelting converters will still be dominated by high-performance magnesia-chrome refractories. High-performance magnesia-chrome refractory bricks are required to have good corrosion resistance to converter media, high high-temperature strength, and good thermal shock stability. China has abundant magnesia resources, and the production process of magnesia-chrome refractories has matured. Therefore, refractory materials for copper smelting converters can choose high-quality and inexpensive magnesia-chrome refractory bricks materials.
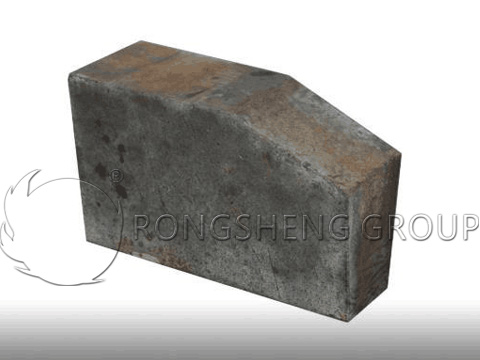
How to Improve the Service Life of the Lining of the Copper Smelting Converter?
Because the converter smelting conditions are harsh, the temperature is high, the chemical reaction is intense, the rapid cold and rapid heat, and the mechanical erosion are all factors that cause the converter smelting production cycle to be short.
In recent years, China has made great efforts to improve the lifespan of converters, rectifying and improving the whole process from refractory materials, furnace and its refractory lining building quality, and standardization of smelting operations. The service life of copper smelting converters has been greatly improved compared with traditional converters. Free to get the prices of the refractory materials, Please contact us as follows.