Corundum-mullite castable is a refractory castable made of dense corundum and mullite as aggregates and white corundum powder, α-Al2O3 micro powder, and mullite powder as fine powder. Corundum mullite refractory castable manufacturer, Rongsheng refractory material manufacturer, free price consultation, free design of refractory lining solutions.
Corundum-Mullite Refractory Castable
Corundum-mullite refractory castables, the mullite raw materials selected in the ingredients are all artificially synthesized. It has the characteristics of high melting point, creep resistance, low expansion coefficient, thermal shock resistance, and excellent corrosion resistance. When the temperature rises during use, the strength and toughness of mullite not only do not decrease but are greatly improved, it is widely used in the refractory industry. But the difference between corundum and mullite lies in the hardness and density of corundum. Compared with mullite, the performance of corundum is better than that of mullite. After the castable is fired at a high temperature, it has higher refractoriness, mechanical strength, and a higher load softening temperature. Therefore, corundum-mullite castables can be widely used in refractory products lining furnaces in various industrial furnaces with severe conditions such as high temperature, erosion, and erosion.
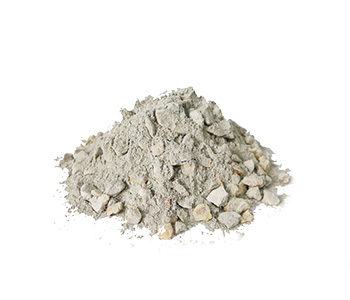
Functional Characteristics of Corundum Mullite Castables
- (1) It has the advantages of both corundum castable and mullite castable.
- (2) High high-temperature strength, good thermal shock resistance, and structural shedding resistance.
- (3) Good thermal shock resistance and high load softening temperature. The high-temperature creep rate is small and the chemical corrosion resistance is good.
Corundum-mullite castables can be used in the front and rear kiln mouths of large cement kilns, coal injection pipes, and other industrial kiln burners and linings. Rongsheng refractory castable manufacturer.
How to Improve the Thermal Shock of Corundum Mullite Castable?
Corundum-mullite castable has the characteristics of high load softening temperature and good creep resistance among high-temperature refractory materials. However, pure corundum products have less than ideal thermal shock resistance due to their large thermal expansion coefficient. Pure mullite products have a smaller thermal expansion coefficient and better thermal shock stability.
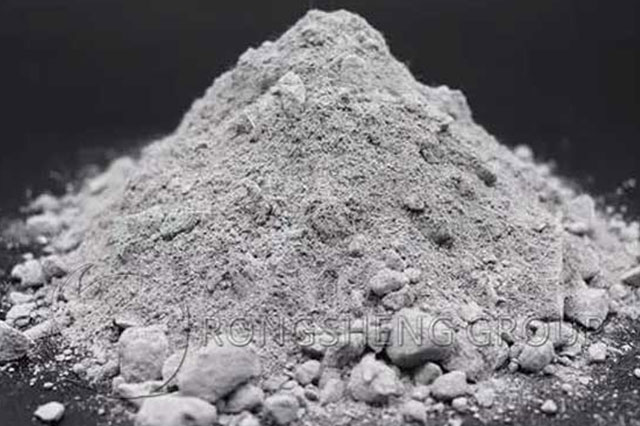
Corundum-mullite castable is made of mullite and corundum. When the mass ratio of mullite and corundum is 75:25, it is exactly at the combination point where the eutectic ingredient composition point appears at 1840°C in the SiO2-AL2O3 phase. If the thermal shock is increased, the best ratio of mullite to corundum is 75:25. Because the thermal expansion coefficient of mullite is smaller than corundum, and the thermal expansion coefficient of composite materials is greater than the former. The thermal expansion coefficient between mullite and corundum causes thermal expansion inside the composite material, which will form micro-cracks, increase the material’s fracture absorption energy, and improve the thermal shock resistance of the castable.
If the ingredients are combined at the eutectic point, it will affect the creep resistance of the castable, and the creep rate is minimal at this time. When the ratio of mullite to corundum is about 75:25, the aggregate has a greater impact on the thermal expansion coefficient and thermal expansion mismatch of the product. When fine cracks occur in the castable and are subjected to thermal shock stress, the fine cracks will expand, and at the same time, the aggregate will undergo transgranular fracture and consume a large amount of energy. It not only inhibits the expansion of main cracks but also affects the thermal shock stability of corundum-mullite castables.
Of course, corundum castables are also made, and their thermal shock resistance is also very good. The reason is that the different proportions of aggregate and binder lead to differences in thermal shock stability. The thermal expansion coefficient of corundum-mullite castables has a great influence on thermal shock stability. Microcracks caused by thermal expansion mismatch can actually improve the thermal shock resistance of castables.
To sum up, when the ratio of mullite and corundum is 75:25 in the process, the thermal shock stability is the best. The apparent porosity is about 20%, which is very beneficial to the thermal shock stability of the castable. Therefore, the apparent porosity of corundum mullite castable is controlled at about 20%, which further improves the thermal shock stability.